Preface
and Acknowledgments
The
seminal inspiration for this paper is
the work of Michael W. Sherman, who,
in collaboration with William Moran
and Kurt Nauck, has presented the evolution
and development of the labels used by
the Victor Talking Machine Company and
its successors. It was felt that a similar
effort should be given to the introduction
and evolution of record labels used
by the Gramophone Company of London,
its sister companies and its successors
during the acoustical recording era.
This document will attempt to place
those labels that have been seen, either
directly or indirectly, in some sort
of chronological order, and to show
the variations in colors, sizes, and
other aspects, together with the reasons
for and, where ascertainable, the times
of these variations.
To
my knowledge there has never been a
book or other document devoted to the
evolution and chronology of the labels
used by the Gramophone Company, its
sister companies, and successors. It
has come to my attention that at one
time there was in the EMI Archives a
book which contained all of the labels
actually used, as well as those designed
for use, by the Gramophone Company.
This book has since been moved to EMI
Headquarters, and is no longer available
for viewing. This paper will perforce
deal with such labels as have been seen
or made available to me during the course
of this research.
Many
of the images shown throughout this
paper have been copied from records
placed for sale or auction on various
Internet sites. As such, they do not
always appear in pristine condition.
Many others are from my own collection.
Still others have been borrowed liberally
from various publications, with my grateful
thanks and apologies to any authors
who take exception, and in the hope
that their further dissemination will
stimulate further interest of current
and potential collectors and devotees.
I
am sincerely grateful for the many items
of information relative to the labels,
methods, institutions, and historical
information described in this paper.
The donors, collectors, and dealers
throughout the world are too numerous
to mention, although I have tried to
give credit to the major contributors
throughout the following sections. Among
the many dealers from whom I have borrowed
images of labels, as well as being the
recipient of their knowledge, are Sergio
Alfonsi, Carlos M. Ballester, Omar Facelli,
Raymond Glaspole, Lawrence Holdridge,
Rainer Lotz, Kurt Nauck, Rudi Sazunic,
and Andreas Schmauder. As with many
papers of this nature, the contributions
from the publications listed in the
Bibliography, particularly those in
The Record Collector and The Hillandale
News, have contributed numerous tidbits
of information. Of particular value
are the publications and other materials
afforded to me by Alan Kelly, who has
devoted over fifty years to the discography
of over 200,000 recordings made by the
Gramophone Company. I hope that I have
given due credit throughout this paper
to his efforts, as well as to those
of other contributors. Any omissions
are purely unintentional.
Introduction
The
evolution and chronology of labels used
by the Gramophone Company during the
acoustical recording era appear at first
to be extremely complex. These labels
did not evolve in the same manner as
those used by the Victor Talking Machine
Company. Moreover, the designs and printing
of the Victor labels were more centrally
controlled than those of the Gramophone
Company, which printed their labels
in the various cities and locations
of some six or more major manufacturing
plants located throughout Europe and
the Far East. In contrast to their Victor
counterparts Gramophone Company labels
did not progress through any orderly
series of more or less distinct designs,
from the Consolidated to the Colored
Trademark.
The
various Berliner companies in America
(see below) were making flat disc recordings
almost ten years before the Victor Talking
Machine Company made its first recordings
in January 1900. The recording engineers
responsible for making these records
had been trained by Emile Berliner himself,
and were the same ones who went to London
in July 1898 and later. They were responsible
for setting up the recording studios
in London, Hanover, and elsewhere in
Europe, and for developing and refining
the recording methods first established
by Emile Berliner. They included, among
others, Frederick William Gaisberg,
his brother William Conrad Gaisberg,
William Sinkler Darby, and Belford Royal.
Nor should one forget that Emile Berliner
had sent his nephew Joseph Sanders,
whom he had trained in the arts of processing
completed recordings on wax-coated zinc
plates for the manufactured of issued
records. The Hanover plant was manufacturing
finished records for sale from shells
imported from various Berliner companies
in the United States and Canada as early
as April 1898. Even the London recordings
predated those made by Victor by more
than seventeen months.
Gramophone
Company records during the acoustical
era fall into three major categories.
The earliest are the so-called pre-label
E. Berliner’s Gramophone, generally
known as Berliners (August 8, 1898 to
as late as December 1905). These discs
are a nominal 7 inches in diameter,
with no paper labels, but having the
necessary details of the recording inscribed
in the central area by the recording
engineer, his assistant, various technicians
at the processing plant, or a combination
of these. For a short time after June
1901, Berliners were also issued without
labels on 10-inch discs.
The
second group have paper labels bearing
the Recording Angel trademark (see below
under The Recording Angel Trademark),
and include both 10-inch
and twelve-inch discs known as G&Ts
(December 10, 1900 to November 18, 1907)
and GCL’s
or pre-DOGs (November 19, 1907 to February
1909), respectively. The third group
carries the "His Master’s Voice"
or DOG trademark, first known as HMV
Concerts or DOG Concerts for 10-inch
discs and HMV Monarch or DOG Monarch
for 12-inch discs, respectively, from
February 1909 to August 1910, and later
as HMV’s from August 1910 to the end
of the acoustical era, about April 1925.
These can be subdivided further according
to various properties described below
under "His
Master’s Voice" Trademark.
Even within these parameters, numerous
variations and exceptions exist.
One
must also consider the labels used by
the sister companies, as well as those
of various successors. The former include
the International Zonophone Company
of Berlin, following its purchase by
the Gramophone Company in June 1903.
An offshoot of this purchase resulted
in the formation of the British Zonophone
Company in 1909. We have included also
labels used by the Deutsche Grammophon
Gesellschaft, the company formed by
the German government following the
outbreak of World War I and the subsequent
seizure of all assets of the Deutsche
Grammophon Aktien-Gesellschaft, viz.,
Stock Company, which was the German
branch of the Gramophone Company. These
labels also extend to those used by
the Opera Disc Company of New York,
which acquired numerous Gramophone Company
metal parts by purchase after the end
of World War I.
Historical
Background
Emile
Berliner (the founder of the feast!)
began working on the development of
a recording machine in Washington D.C.
after having seen the Graphophone unveiled
by Tainter and Bell in 1886. He showed
an early device to the patent attorney
Joseph Lyons by April 1887, which recorded
a lateral pattern on lamp-blacked paper
wrapped on a cylinder, similar to the
phonautograph of Leon Scott, but with
an oil mixed with lampblack applied
to the surface to make a fatty ink better
able to be engraved with a cutting stylus,
then producing a stereotyped copy engraved
into metal by a photoengraving process,
and played back on another device with
a stylus following the lateral grooves
and making a diaphragm vibrate.
By December 1888 Berliner had improved
his device sufficiently to begin making
plans for sale to the public. By July
1889 he was using hard vulcanized rubber
rather than celluloid for his disc copies.
He departed on a trip in August 1889,
and gave a demonstration of his device
on November 26, 1889 at the Electro-Technical
Society in Berlin. The first pressing
of 25,000 single-sided 5-inch Berliner
discs was made in Europe in late 1889,
but "the sound quality was so dubious
that a small rectangular paper label
imprinted with the actual words was
glued to the back." (Koenigsberg
1990 p. lvi)
According
to Raymond Wile, "It was in Germany
that the first commercial beginnings
of the gramophone occurred - presumably
in July 1890. The toy makers Kammer
and Reinhardt in Waltershausen (Thuringia)
began to market small hand-propelled
gramophones and a talking-doll….For
an additional price, zinc discs also
were available. The records were produced
by two companies, one known solely by
the initials GFKC, the other was the
Rhenische Gummi und Celluloid Fabrik
Werkes of Necharan, Mannheim. The machines
and records also were imported into
England, notably by J. Lewis Young,
but were available for only a few years
in both countries" (Wile 1990 p. 16).
Berliner's efforts led to the establishment
of Deutsche Grammophon Gesellschaft
(DGG, later to become Polygram).
In 1891 Berliner paid a New York clock
maker to produce a spring mechanism
to power his gramophone, and on April
23, 1891 he created the short-lived
American Gramophone Company. In 1892
he organized the United States Gramophone
Company in Washington, D.C., marking
the beginning of the record industry
that would spread around the world.
All of Berliner’s patents were assigned
to that company, and thus became corporate,
rather than individual assets. In April
1893 Berliner transferred all patents
to a new company, the United States
Gramophone Company at 1205 G Street
NW in Washington D.C., and hired Fred
Gaisberg to record talented singers
and other artists.
In
1894 Berliner opened a factory and showroom
at 109 North Charles Street in Baltimore.
The flat record size was standardized
at 7 inches, and 2 gramophone models
were produced with electric motors in
addition to the hand-cranked model.
By the fall of 1894, Berliner published
his first list of gramophone discs for
sale, at 60 cents each, 6.875-inch diameter
(after 1895 7-inch), 2 minutes in duration,
made of celluloid (after 1895 in hard
vulcanized rubber), one-sided, with
name and date stamped in the center
(paper labels after 1900.)
On
February 19, 1895 Berliner received
patent 534,543, filed March 30, 1892.
He signed an agreement with William
C. Jones who organized the new Berliner
Gramophone Company of Philadelphia,
chartered October 8, 1895, and in 1896
sold a territorial license to Frank
Seaman who formed the National Gramophone
Company of New York on October 19, 1896
to expand the sales and production of
gramophones and records to sell records
and machines in New York and New Jersey.
"Berliner's best year for record sales
was 1898 when he sold, mainly through
Frank Seaman's National Gramophone Co.,
713,753 discs" (Koenigsberg, 1990, p.
xxxvii). Other licenses were sold to
the New England Gramophone Company and
to the Berliner Gramophone Company in
Great Britain, founded by William Barry
Owen in 1897.
Having obtained various patents in Germany
and England in 1887 and in Italy, France,
Belgium and Austria in 1889, Berliner
sent William Barry Owen, the Sales Director
of the National Gramophone Company,
as his agent to London in July 1897,
where in May 1898 and together with
Trevor Williams, a barrister, Owen organized
financial backing for and became the
first Managing Director of what was
originally known as the Berliner Gramophone
Company, which had exclusive rights
(from Berliner!) to sell gramophone
instruments and records in Europe. Trevor
Williams became the first Chairman of
the newly established company. The Berliner
name was shortly dropped from the company
name, which became the Gramophone Company
of London.
Berliner
also sent his nephew Joseph Sanders
and Frederick Gaisberg, both of whom
he had trained in the art of making
and reproducing recordings on flat discs.
They embarked for London on July 30,
1898. Gaisberg stayed in London to organize
the recording studio, established at
31 Maiden Lane, The Strand, London,
and assembled from instruments provided
by Eldridge Reeves Johnson (see below).
Joseph Sanders went on to Hanover, Germany
where Emile’s brother Joseph operated
the Telefon Fabrik, a telephone
factory. This was converted to the world's
first shellac record production line,
as the German branch of the Gramophone
Company in Berlin, from which sub-branches
were formed in Russia and Austria. Shortly
afterwards mass production began, and
all finished plates recorded from August
8, 1898 were processed there until the
completion of the pressing plant in
Riga in 1902. From that time forward
all recording locations within the Russian
empire shipped their finished plates
to Riga. Finished plates were shipped
from the recording locations to the
various manufacturing plants as these
became available. Before any other processing
plant was available, labels for use
at the Hanover plant might be in any
of several languages, e.g., English,
Italian, Russian, and so forth.
On
December 6, 1898 Owen established the
Deutsche Grammophon Gesellschaft at
Kniestraße in Hanover, Germany.
In the beginning there were four presses
which had been imported from the United
States. The pressing material was supplied
by Duranoid Company of Newark, and consisted
of shellac, barytes, slate dust and
cow hair. It was to be several years
before the cow hair could he replaced
by cotton flock. At first the masters
also came from the United States, but
soon they also came from England where
Berliner had helped to found the Gramophone
Company, whose purpose was to supply
the whole European market with recordings,
as well as to make use of his various
patents. The first masters brought from
the United States were zinc discs, and
they appear to have been rather delicate;
we are told that damaged matrices could
be repaired with an engraving tool.
However it soon became possible to make
galvanic impressions from the original
recordings by mounting the zinc discs
on rubber plates and brushing them with
powdered graphite, after which copper
masters could be produced in a galvanic
bath.
In
1898 the Berliner brothers installed
ten record presses in Joseph Berliner’s
telephone factory in their native Hanover,
Germany. Arrangements were soon under
way to have records pressed in Hanover
from Berliner matrices either made by
the Gramophone Company of London or
imported from the United States. The
first records were pressed in June 1898.
In 1899 the Hanover plant had fourteen
hydraulic presses together with six
or more electrolytic baths for preparing
the original stampers, and by October
1899 the plant was providing London
with 5,000 records per day. In February
1901, the plant had 40 presses capable
of producing some 14,000 7-inch discs
per day, an average of 350 finished
records from each press. In October
1901 the plant manufactured 24,256 ten-inch
discs, about 800 per day, using the
new ten-inch presses recently acquired
from the Victor Talking Machine Company.
Just over a year later this output had
risen to about 2,000 discs per day.
Due to the necessary differences in
the equipment for manufacturing 7- and
10-inch (and later 12-inch) discs, one
can only conjecture how many of the
forty or more presses were devoted to
each size. One can estimate that one
operator running a single press with
a single stamper or "shell"
could turn out between 350 and 500 finished
records per day, depending on several
factors, including the durability of
the stamper. By the beginning of 1904,
some 25,000 discs were produced each
day. The Hanover factory now had no
fewer than 200 presses and during the
Christmas weeks of 1907 the daily production
was 36,000 discs. In the following year
the total production reached 6.2 million
discs, the highest figure before World
War I.
During
the first foreign or Six Cities tour
between May and August 1899, sales branches
were established in Leipzig, Budapest,
Vienna, Milan, Paris, and Madrid (that
is, in Germany, Hungary, Austria, Italy,
France, and Spain). The Compagnie Française
du Gramophone was established in Paris
in 1899. On January 1, 1900 Deutsche
Grammophon became a joint-stock company,
i.e. Aktien-Gesellschaft (DGA) with
60% of shares belonging to the Gramophone
Company in London, and the trademark
"His Master's Voice" was registered
in the United States Patent Office under
Registration 34,890, July 10, 1900,
under Emil Berliner's name. In 1904
Deutsche Grammophon Gesellschaft moved
to its new facilities at Celler Chaussee
(now called Podbielskistraße.)
In
December 1900 Owen acquired the Lambert
typewriter manufactory for $20,000,
and shortly thereafter changed the name
of the company to the Gramophone and
Typewriter Company. Soon after this
he introduced an electric clock. Both
of these enterprises failed; fortunately,
he did not change the company’s name
again. By the end of 1904, Owen had
sold his interest, resigned his directorship
in the company, and retired to the United
States to raise chickens in the town
of Vineyard Haven on Martha’s Vineyard,
his family’s ancestral home. His departure
ended the company’s infancy and childhood,
and it now entered adolescence.
A
letter on official Head Office stationery
dated November 25, 1904 (see below)
lists Sales Branches in London, Berlin,
Hanover, Paris, (May 1899), Vienna,
St. Petersburg, Moscow, Brussels, Amsterdam,
Stockholm (1903), Copenhagen (1904),
Milan, Barcelona, Lisbon, Sydney, Calcutta,
and Cape Town. Later branches would
be established in Alexandria, Bombay,
Budapest, and Warsaw. Offices were opened
in Japan and China in 1902 and 1903,
respectively. In 1905, daily production
at the Deutsche Grammophon record plant
in Hanover was already 21,000, equivalent
to a yearly capacity of 7-8 million
records, while the plant in Riga managed
to produce 12,000 records per day. Gramophone’s
total production in 1905 was estimated
at 21 million units.
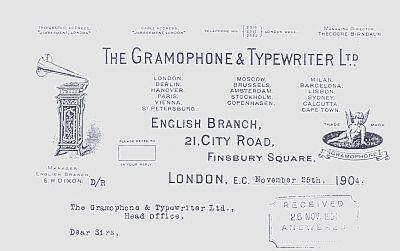
Head
Office letterhead, 1904
By
the end of 1906 it was apparent that
the Hanover factory could not handle
the increasing volume of recordings
that were being shipped to it from all
over the Continent. A new factory was
therefore proposed to be built at Hayes
in Middlesex, England. Ground was broken
on February 9, 1907, and the new factory
was completed by June 1908. By November
of that year it was turning out 165,000
records monthly. (Author’s note: This
figure indicates about 5,500 records
per day with perhaps ten or twelve presses,
and can be compared to the Hanover plant’s
production of 14,000 7-inch discs per
day using 40 presses as early as February
1901.)
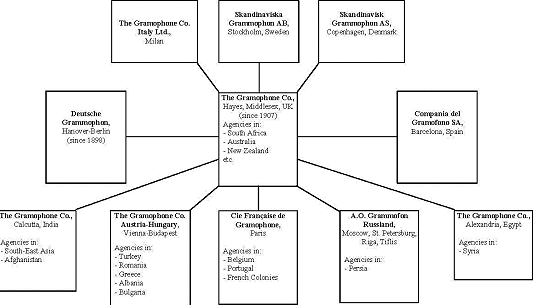
The
global Gramophone Company conglomerate
in 1910.
Click
for enlarged image
By
the summer of 1912 The Gramophone Company
had factories operating in Austria (Aussig),
England (Hayes), France (Ivry), Germany
(Hanover), India (Sealdah), Poland (Warsaw),
Russia (Riga), and Spain (Barcelona).
Distributors were located in Australia,
Ceylon, East Prussia, Holland, Italy,
New Zealand, Persian Gulf, South Africa,
and Tasmania (from the EMI website).
The
Recording Engineers
The
first recording engineer was Frederick
William Gaisberg, a native of Washington,
D.C. Having worked for the Columbia
Phonograph Company where he became proficient
in recording on wax cylinders, he visited
the Berliner laboratory, and was hired
almost immediately and trained in the
art of making gramophone recordings
by Emile Berliner. In July 1898 he went
to England and became the first, and
at that time, the only recording engineer
for the newly formed Gramophone Company
of London. He was soon joined by William
Sinkler Darby and Belford Royal, both
trained by Berliner, and later by his
brother William Conrad Gaisberg. These
four engineers were responsible for
some 21,000 recordings on 7-inch tablets,
49,500 on 10-inch tablets, and 12,500
12-inch recordings, a total of over
83,000 recordings. Belford Royal made
many recordings, usually in association
with Will Gaisberg, and his suffix R
is found frequently on these discs.
Between
August 8, 1898 and the spring of 1900,
a total of just over 7,600 recordings
were made on 7-inch wax-coated zinc
plates, better known as "zincs."
They can be classified as follows.
Series |
Dates |
Location
|
Engineer |
Number |
"original"
|
8
Aug 1898 - 31 Oct 1898 |
London
|
FWG |
406 |
"unlettered"
|
1
Nov 1898 - Jun 1900 |
London |
FWG |
2089 |
No
matrix |
30
Mar 1899 - 25 Apr 1899 |
St.
Petersburg 1st |
WSD
|
245 |
Suffix-A |
Dec
1899 - Dec 1900 |
St.
Petersburg 2nd |
WSD
|
2449 |
Six
Cities |
17
May 1899 - 10 Aug 1899 |
|
FWG
and WSD |
1433 |
British |
5
Sep 1899 - 11 Jun 1900 |
|
FWG
|
1041 |
All
subsequent recordings during the acoustical
era were made on all-wax tablets. The
early itineraries are as follows.
Fred
Gaisberg
(with George
Dillnutt)
|
1
May 1900 – Sep 1906
|
7-inch
|
FWG
|
6,977
|
8 Apr 1901 – 3 Jul 1919
|
10-inch
|
FWG
|
20,590
|
Feb 1902 – Jul 1919
|
12-inch
|
FWG
|
3,406
|
Far
East Tour
|
Nov 1902 – Jun 1903
|
&"
and 10"
|
FWG
|
1,843
|
Suffix
d/e/f series
|
Oct
1903 – 26 Nov 1908
|
All
sizes
|
WCG
|
33,580
|
Suffix
g/h/i/ (B/x/y/
|
1901 – Sep 1909
|
All
sizes
|
WSD
|
12,054
|
Of
the next four recording engineers, Franz
and Max Hampe supervised some 36,000
recordings, largely in Germany, the
Scandinavian countries, and Eastern
Europe, while Cleveland Walcutt and
Charles Scheuplein were responsible
for over 14,000 recordings, mainly in
France, Spain, the Netherlands, and
Belgium. Further details of these
and additional recording engineers and
their recording sessions in various
locations may be found in detail in
Alan Kelly’s catalogues.
Manufacturing
Methods
Following
the successful invention of a machine
for recording sound on flat discs and
of another machine to replay these discs,
numerous rival companies arose in both
the United States and Europe, ready
to compete with the Berliner companies.
The competition was not only fierce
─ it was cutthroat, to the extent
that even the patents applied for and
received by the various participants
barely indicated the actual composition
of the materials used, nor their size,
shape, dimensions, or other qualities,
conditions, and specifications that
might be useful to other interested
parties. In other words, corporate espionage
was rampant in this budding and rapidly
expanding industry! Moreover, certain
unscrupulous individuals who had been
employed in Berliner’s laboratory and
made privy to various trade secrets
later applied for patents based on various
aspects of his methods! Much of what
we know today of the methods and materials
used more than a century ago has been
derived by inductive reasoning from
two major sources, viz., the metal parts
and machines that have survived and
the records themselves. Much of the
information presented here and in other
related documents is derived from the
direct examination of these surviving
items. Another important source of information
is the surviving correspondence between
officers and employees of the Gramophone
Company’s Head Office and those in the
various sales offices and manufacturing
plants and branches throughout Europe,
Africa, and the Far East.
Over
the half century or more during which
78rpm discs were recorded both acoustically
and electrically, numerous changes were
made in both the various steps of record
production as well as in the materials
and machinery used. These will be presented
in more detail in the following paragraphs.
As an early example, in a manuscript
dated November 21, 1897, Berliner described
the making of a matrix, viz,
The zinc record is mounted on a tablet
of hard rubber with a thin sheet of
gutta percha with moderate heat and
pressure. Connection by wire having
been made previously the zinc is cleaned
with strong alcohol, lye and whiting
[a mixture of 85-90% fine calcium
carbonate and boiled linseed oil],
carefully rinsed and brushed with
soft brush. It is then suspended for
10-15 seconds in a moderately strong
cyanide of potash in water solution
and a current of about amperes using
the zinc record as anode and a piece
of carbon as cathode. It is then put
into a bath prepared as follows.
Cyanide
of copper bath
Dissolve 8oz. of best cyanide of potash
per gallon of water. To a saturated
solution of sulphate of copper add
enough concentrated ammonia to barely
re-dissolve the ammoniaret of copper.
Add enough of this copper mixture
to the cyanide solution - - stirring
constantly - - until a light amethyst
color is obtained. Add this to either
cyanide of silver or gold or both
just enough to enoble the solution
or more at pleasure.
Into this bath immerse the zinc disc
after use of soft brush using a carbon
hard retort and silver anode and a
current of about amperes. Leave 5
minutes, brush with whiting and nickel
in ordinary nickelbath using at least
5 volts tension. Leave in nickelbath
about 5 minutes. Take out, brush strongly
with whiting, screw around disc a
hard rubber flat ring and put in sulphate
of copper depositing tank (current
on) of about 18º density.
Deposit from 5 to 7 days (and nights)
using about 4 amperes and about ¾
volt
per tank with constant agitating device.
When thick enough detach, turn off
edge and back to standard size and
etch zinc off from the copper deposit,
then nickel in ordinary manner.
The cyanide copper bath after being
freshly made contains free ammonia
which should be nearly gotten out
by continued stirring.
(The
above was published previously in The
Hillandale News, Vol. 138, page
36, June 1984, and affirms that the
initial copper shell was reinforced
further with a layer of nickel.)
Between
August 8, 1898 and May 1900 all Gramophone
Company recordings were made on 7-inch
wax-coated zinc plates. During that
period Frederick William Gaisberg and
William Sinkler Darby were the only
recording engineers known to be employed
by the Gramophone and Typewriter and,
although not always mentioned, each
appears to have had an assistant who
was responsible for "keeping the
record straight," that is, entering
the correct information for each recording
into the Weekly Return (see below under
Recording Locations), which included
the title of the selection, the artist’s
name, the recording location, and usually
the recording date. He was probably
responsible also for entering the same
information in the central area of the
finished recording, together with the
daily matrix or serial number and the
catalog number, although sometimes this
was done by the engineer.
Before
being shipped to Hanover, Germany, the
finished recordings were "fixed"
by etching them in an acid solution
of sodium dichromate, and then dipping
them in an organic solvent to remove
the remaining wax. Some sources say
that the backs of the finished plates
were coated with varnish before "fixing,"
but this appears to have been unnecessary,
since the dichromate wash generally
took less than fifteen minutes. At the
processing plant the zinc plates were
subjected to electrolysis, also called
electroplating, electrodeposition, and
galvanization, by which a film of metal,
usually from a copper and later a nickel
anode, was deposited onto the original
master recording, which served as the
cathode, to produce a negative mirror
image, much as described in Berliner’s
manuscript of 1897 cited above. This
metal film, of proper thickness, usually
about 1/16 inch, and backed with further
metal as necessary, was the "shell,"
a negative image of the original recording.
In most instances it was the sole copy
of the original, which could be subjected
to repeated electrolysis to provide
additional shells as these wore out.
The shell was used to press positive
finished records until it wore out.
The original recording might then be
used again to produce a secondary shell,
from which additional finished records
could be stamped. When the original
recording itself was no longer useful,
and if additional issued records were
required by dealers, the artist was
often asked to return to the studio
and re-record the selection. This practice
was done frequently in the United States.
From
Alan Kelly’s Holland Catalogue:
"The
techniques of record making also changed.
To make a record on a zinc plate the
expert had to clean the plate and
then coat it with beeswax. Before
use, he had to warm it and moisten
it with alcohol to provide the cutting
stylus with as free a run as possible.
The stylus was affixed to a diaphragm
that vibrated in sympathy with the
sound waves of the song and music,
sung or played into the large mouth
of a horn. After recording, he had
to develop the plate by placing it
in a bath containing a chromic acid
solution for about ten minutes, and
then wash and dry it before it was
in a suitably safe state to be crated
for dispatch to Hanover. Such discs
could be played back immediately.
The
new wax blanks still had to be warmed
but they arrived from the factory
almost ready for use. (One may assume
that the blank wax recording tablets
were prepared at the Hanover plant,
and shipped to the location of the
recording engineer.) The composition
of the wax varied according to the
recording location and the time of
year ─ softer wax would be required
in winter in Finland and harder wax
in summer in India. The processing
however was by electroplating and
this was done at Hanover so that the
expert was no longer troubled by complaints
from hotelkeepers and their guests
about the injurious effects of leaking
acids. Although the recorded surface
of the wax matrix was fragile and
could easily be damaged by even slight
contact, the blank itself was over
an inch thick and with properly designed
packing was well able to survive the
rigors of rail and sea travel. Most
of them did, though a few arrived
cracked and unusable."
Following
the expiration of Bell and Tainter’s
patent rights for all-wax recording
on May 1, 1900, the Gramophone Company
introduced the all-wax recording tablet
in June 1900. Finished recordings were
sent to the processing plant with the
matrix/serial number, the selection,
the artist’s name, the recording location,
and the recording date inscribed on
them, but without the Berliner logo
or the Recording Angel trademark. At
the processing plant, the associated
information from the Weekly Return was
entered into the appropriate Register,
and each wax tablet was coated with
fine graphite to allow it to conduct
electricity. It was then subjected to
electrolysis as described above. The
"shell" so obtained was then
used to provide "a carefully pressed
black shellac record," containing
only the recording and the serial number,
as an exact duplicate of the original
wax recording tablet, which was usually
distorted or destroyed during the electrolytic
process. There is some evidence that
a "second shell" was occasionally
obtained from the wax tablet, but in
most cases the latter was rendered unusable.
The wax recording tablets were about
one inch thick, but the surface was
still subject to distortion when the
metal shell was separated from it.
The
black shellac record, which is equivalent
to Alan Kelly’s "COpy matrix,"
was treated in the same manner as the
original wax tablet, to produce the
first stamper. It was also in effect
the equivalent of Eldridge Johnson’s
"mother" part, except that
it was shellac rather than metal. The
Berliner logo and the Recording Angel
trademark were now embossed on the stamper
together with the assigned catalog number;
the stamper was then ready to be used
to press finished and issued records.
In
his brief summation of the history of
the Berliner companies in North America,
Michael Sherman makes the following
comment in reference to the need for
additional "takes" being made
for popular selections. Thus,
"In
addition, pressings were occasionally
made on a special thick, hard rubber
blank which enabled the creation of
a new stamper. Complaints about the
‘groove spread’ on the pressings curtailed
this process, though it is believed
that the small ‘2’ sometimes found
on Berliners indicated the use of
this technique."
This
provides further confirmation that the
various Berliner Gramophone companies
in North America were using a form of
Copy matrix system to produce
secondary stampers as early as 1895.
Each
zinc plate was just under 7 inches (some
17.7 cm.) in diameter and about 0.0196
inch (0.5 millimeter) in thickness,
and weighed just under four ounces,
approximately one-quarter pound. To
travel with 500 or more of these plates,
as was usually the case, would add some
125 pounds of baggage, and occupy less
than one-half of a cubic foot of space,
roughly 7x7x10 cubic inches! They appear
to have been packed into wooden crates
holding 50 plates each. To prepare the
discs for use, they would have to be
brushed with a solution of suitable
wax compounds in alcohol and allowed
to dry. In his patent U.S. No. 382,790,
dated May 15, 1888, Emile Berliner states
that, "a plate or cylinder so prepared
may be preserved indefinitely, and is
at all times in good condition to received
the phonautographic record." This
would require additional baggage in
the form of such a solution, as well
as the highly corrosive solution of
sodium bichromate in a sulfuric acid
solution, necessary for the initial
etching of each plate following the
completed recording. Additional pure
alcohol would also be required to remove
the excess wax during the recording
process as well as from the finished
and etched recording plate.
The
need for the two latter items was eliminated
with the introduction of the all-wax
recording tablet, reputedly by Eldridge
Reeves Johnson, president and founder
of the Victor Talking Machine Company
of Camden, New Jersey. These were approximately
one inch in thickness and about twelve
inches in diameter, each weighing about
26 ounces, or a little over one and
one-half pounds. In terms of baggage,
500 of these tablets would weigh approximately
800 pounds, and occupy some 45 cubic
feet of cargo space, and such space
would have to be cold enough to maintain
the solidity of the tablets without
their melting! As indicated below, they
were packed in wooden packing cases
holding 30 to 50 blanks, weighing between
40 and 80 pounds each.
There
is evidence that the thickness was reduced
to three-quarters of an inch at some
later date. Whether the diameter of
wax tablets was altered over the years
is unknown to the author. The use of
wax for recording on cylinders had been
suggested by the Volta Laboratory of
Washington, D.C., as early as 1885.
Volta brought this suggestion to Thomas
Edison, who turned it away. The use
of wax cylinders then devolved to the
Columbia Phonograph Company, licensed
in Washington, D.C., in 1889.
More
than a quarter-century later, R.E. Beckett,
a recording engineer on his three month
sojourn in India and the Far East in
a report dated June 14th,
1929 wrote:
The
apparatus and personal baggage weighed
approximately one and a half tons.
Considerable weight could be reduced
by establishing suitable centres for
storing spares, i.e., Bombay, Calcutta,
Singapore. It takes 14 days to get
spares from Calcutta to Java by the
quickest route.
Steps
were taken to reduce weight, by having
machine stands for each recording
centre. Therefore I suggest (the)
same could be done with regard to
the wax cupboards and other heavy
accessories at present being transported.
The apparatus continually arrives
at its destination in a damaged condition,
although every care was taken with
the packing. It took several days
during the Bangkok session to repair
broken parts.
Blanks
were usually despatched to the Far
East in common wooden packing cases,
containing 30 to 50 blanks, these
cases were nailed down, and a considerable
time was spent by the recorder every
morning, in opening them, and again
each evening in packing the scrap
and originals. From 30 to 50 originals
and approximately 15 scrap were made
each day.
Every
morning, before recording, the floor
was swept by the engineer to prevent
the excessive dust from getting on
the surface of the waxes. A man could
be employed at each centre, for the
packing of blanks, cleaning the studio
and helping with the heavy work generally.
The
representatives in Rangoon, Calcutta,
Bombay and Lucknow complained of the
number of records that they were expected
to make, and in the case of the Lucknow
records, the agent said that out of
the 800 made, only about 250 were
anticipated to be good sellers.
Very
little attention could be made to
individual records, owing to the large
number made per day; therefore, no
extra time was possible on the more
important singers. With regard to
one operator doing the Eastern recordings,
and in view of the present amount
of records required by the Calcutta
branch, I consider this to be unadvisable.
During my stay in India, the electrical
engineer marked the blanks, and did
most of the booking that was necessary.
He also had to spend a considerable
amount of time attending to batteries
before and after the session. If this
work becomes part of the recorder's
duty it would mean less time for actual
recording.
From
the detailed summary of work in this
report, it is clear that during his
four and a half month tour Beckett worked
an average of six days a week and was
sick for three days with 'fever'. Working
alone, Beckett had to arrange all shipping,
undertake running repairs, find his
own accommodation in each city, deal
with Customs officers, sea captains,
local traders, agents and artists, as
well as the job of actually making recordings.
Beckett had joined the Gramophone Company
in 1919 as a mechanical draughtsman,
left to work elsewhere then rejoined
in 1922 as one of some eight recording
engineers working between 1921 and 1929.
He toured Europe and Africa, visited
Egypt and Iraq as well as India and
the Far East. He then spent 9 years
resident in Berlin, leaving only upon
the outbreak of war. Spending the war
years as Joint Night Manager at Hayes,
he re-transferred to the Recording Department
in 1945.
When
Johnson’s 5-stage manufacturing process
was introduced in 1903, the first negative
metal part from the original wax tablet
was still the "shell," and
contained only the recording and the
serial or matrix number. The difference
between this process and the Gramophone
Company’s previous method was that all
shells from recordings made after this
time were now used to prepare a positive
metal part by electrolysis, and
this became Johnson’s "mother"
part. Since the "mother" was
produced by electrolysis, the shell
could be used repeatedly to produce
more mother parts, and each mother could
be used to produce multiple stampers
(Author’s note: the three metal parts
of the five-stage process have been
referred to as "father," "mother,"
and "daughters," the last
being the stampers).
The
first manufacturing process described
above produced 7-inch Berliner records
without paper labels. The last two processes
both produced finished records with
paper labels. Since both the black shellac
record in the second process and the
"mother" part in the third
process bore only the matrix number,
the catalog number and any other necessary
information were embossed into the stampers
following their production from
the mother or duplicate shell. When
the label position (see below) was raised
above the record surface some time between
April 11 and August 1902, the matrix
number was no longer visible through
the label, and had to be entered in
the runoff area (see below under Label
Positions). The recording engineer
or his assistant then entered the matrix
number in the runoff area near the edge
of the recorded area, rather than in
the central area. Similarly, as new
stampers were required, both the catalog
and matrix numbers were entered in the
runoff area, thus accounting for the
various locations and different fonts
noted for these numbers.
The
most critical stage in the manufacturing
process was the placement and drilling
of the central hole in each stamper
before it was placed into use. By 1942
that was done by observing through a
magnifying glass the movement of the
ridges on each stamper as it was mounted
on a rotating turntable. When the stamper
was placed so that the ridges no longer
wobbled from side to side, the central
or spindle hole was drilled into the
stamper in its exact center.
By
October 1896, Berliner had changed from
vulcanized rubber to shellac records,
using material from the Duranoid Co.
of Newark NJ. On July 7, 1898, Berliner
contracted with the Burt Company, makers
of billiard balls, to provide record
material in preference to that of the
Duranoid Company. In a letter to William
Owen dated July 30, 1898, Berliner said,
"I
have carefully read all you say about
record pressing and I am very sure
that you undervalue the superiority
of Burt records so far as his samples
show over the Duranoid records. I
hardly think that you have in mind
the fact that after Duranoid records
have been used 50 times they show
an undoubted roughness and rapidly
wear out and become anything but a
recommendation for the Gramophone.
The argument has been made that when
the records are worn out people will
buy new ones but I believe you will
side with me in protesting to this
as a dangerous plea. People should
buy new records on account of the
enjoyment they get out of the old
ones and the longer these remain in
good shape and are shown to admiring
friends the better for the Gramophone
business. It has taken me a great
deal of diplomacy to get to the arrangement
which I have made with Burt. He is
a man way ahead of Duranoid….If Burt
records wear only twice as long as
Duranoid then I say most emphatically
let us pay two or three cents apiece
more for them. Furthermore by Burt’s
system the matrices are much better
preserved than by the Duranoid system."
Information
from a company presently (2007) making
vinyl records from original wax or lacquer
master recordings indicates that the
original recording is plated with a
thin layer of silver, which is then
electroplated with nickel to the thickness
of about fifteen thousandths (0.015)
of an inch. This plate, called the father
plate, is then plated again,
to produce as many as ten positive metal
parts, known as mother plates.
Each mother is then plated again, and
can produce up to ten negative metal
parts known as stampers. Each
stamper can produce up to 1,000 vinyl
records. Thus one father plate can produce
up to 100,000 finished records. This
series of manufacturing steps has been
used almost unchanged during the past
century or more, except to refine the
materials and machinery used for the
several steps.
About
the most succinct way of looking at
the manufacturing process is as follows:
A
recorded wax is first metalized [by
coating it with carbon powder]
by the latest scientific electrical
process. It is then placed in a deposition
bath of copper sulphate solution,
and connected to an electrical circuit
as the cathode, while copper anodes
maintain the copper in the bath. The
wax, in the same way that a magnet
attracts steel, attracts the copper
in the bath, which flies to the metalized
wax face. After twelve hours a sheet
of copper has been grown, and is known
as the "Master." This sheet
is stripped from the wax, and on it
is the negative impression of the
original sound wave grooves. As the
sounds stand up from the surface of
the copper shell, it would not be
possible to play this impression.
A great many duplicates are required
to produce the large number of records
demanded by the public, and therefore
the Master [also
called the "shell" or original
stamper] is
placed in the deposition bath and
another impression is grown in the
same way as before. This is a positive
[equivalent
to the "mother"],
and again, by the same process, final
working shells are grown. These are
"stampers," and are therefore
negatives. To obtain the necessary
thickness for production purposes,
a copper back plate is soldered on.
From this negative stamper the record
is pressed with positive grooves as
on the original wax.
Pressings
are not taken from the Master, because
a knock on the working face would
destroy the recording. Fresh copies
can be grown from the "Mother,"
or positive, and if the latter is
damaged, another can be drawn from
the Master. The average life of each
stamper gives several thousand records.
The stamper then passes to the press
room, where it is fixed in a hydraulic
press together with the corresponding
stamper for the other side of the
record, one stamper being fixed to
the bottom jaw of the press, and the
other to the top. Each is in direct
contact with a metal die, which is
a block of metal drilled to take a
grid of pipes. These pipes are attached
to the heating and cooling system,
and operated by a valve which at a
given moment closes the steam and
allows cooling water to circulate
through the pipes.
Each
pressman has a supply of record material
biscuits, which are of the necessary
size to produce one record. The material
is composed of shellac and a specially
selected "filler." The biscuits
are placed on a heater and brought
to a temperature of 250oF,
and the material becomes of a putty-like
consistency. The pressman places a
label face downwards on the centre
of the bottom stamper, puts the softened
material on top of this, and the label
for the other side of the record face
upwards. The jaws of the press are
closed, one stamper being directly
above the other, and the hydraulic
pressure released, so that the bottom
stamper moves towards the top with
a pressure of a ton to the square
inch. At the same time the cooling
water valve is operated, and the trapped
material between the stampers is cooled
down to a solid state. After thirty
seconds the pressure is released,
the press opened and the record, complete
with labels, ready for removal to
the edging department, where the edge
is removed. Experts minutely examine
each record for flaws, and if it is
passed it is placed in an envelope
and sent to the assembly department
to await orders from dealers
The
following extract is adapted from the
Wikipedia website, http://en.wikipedia.org/wiki/Gramophone_record#Shellac
December 2007, especially for the manufacture
of long playing records:
For
the first several decades of disc
record manufacturing, sound was recorded
directly on to the master disc
(also called the matrix, sometimes
just the master) at the recording
studio. From about 1950 on (earlier
for some large record companies, later
for some small ones) it became usual
to have the performance first recorded
on audio tape, which could then be
processed and/or edited, and then
dubbed on to the master disc.
A
record cutter would engrave
the grooves into the master disc.
Early versions of these master discs
were soft wax, and later a harder
lacquer was used….Sometimes the engineer
would sign his work, or leave humorous
or cryptic comments in the run-off
groove area, where it was normal to
scratch or stamp identifying codes
to distinguish each master.
The
soft master known as a lacquer would
then be silvered using the same process
as the silvering of mirrors, commonly
the lacquer was sprayed with a saponin
mix, rinsed, spraying with Stannous
Chloride which sensitized the surface,
rinsed again before the finally simultaneously
spraying the Silver solution and dextrose
reducer. This silver coating provided
the conductive layer to carry the
current for the subsequent nickel
plating electroplated with a metal,
commonly a nickel alloy. In the early
days (1940-60) the nickel plating
was only brief, just an hour or less,
before transferring to a copper plating
tank. This was due to copper plating
being both quicker and simpler to
manage at that time. Later with advent
of Nickel Sulphamate plating solutions
all matrices were solid nickel. Most
factories transferred the Master Matrix
after an initial flash of Nickel in
a slow warm nickel electroplating
bath at around 15 ampere to a hot
130 degree Nickel plating bath where
the amperage would be raised at regular
intervals until the amperage reached
between 110A and 200A depending on
the standard of the equipment and
the skill of the operators. This and
all subsequent metal copies were known
as matrices. When this metal master
was removed from the lacquer (master),
it would be a negative master
or Master Matrix, since it was a negative
copy of the lacquer. (In the UK, this
was called the master; note the difference
from soft master/lacquer disc above).
In the earliest days the negative
master was used as a mold to press
records sold to the public, but as
demand for mass production of records
grew, another step was added to the
process.
The
metal master was then electroplated
(electroformed) to create metal positive
matrices, or "mothers". From these
positives, stampers (negative)
would be formed. Producing mothers
was similar to electroforming Masters,
except the time allowed to turn-up
to full amperage was much shorter
and the heavier Mothers could be produced
in as little as one hour and stampers
(145 grams) could be made in 45 minutes.
Prior to plating either the Nickel
Master or Nickel Mother it needed
to be passified to prevent the next
matrix adhering to the previous matrix.
There were several methods used, EMI
favoured the fairly difficult, Albumin
soaking method where as CBS Records
and Phillips used the Electrolytic
method. Soaking in a dichromate solution
was another popular method. The electrolytic
method was similar to the standard
electrolytic cleaning method except
the cycles were reversed finishing
the process with Matrix as the anode.
This also cleaned the surface of the
matrix about to be copied. After separating
from the Master a new mother was polished
with a fine abrasive to remove or
at least round-off the microscopic
"horns" at the top of the grooves,
produced by the cutting lathe. This
allowed the vinyl to flow better in
the pressing stage and reduced the
non-fill problem. Stampers produced
from the mothers after separating
were chrome plated to provide a hard
stain-free surface. Each stamper was
next centre punched, methods used
included aligning the final locked
groove over three pins or tapping
the edge while rotating under the
punch until the grooves could be seen
(through a microscope) to move constantly
towards the centre. Either method
was quite skilled and took much effort
to learn. The centre punch not only
punched a hole but formed a lip which
would be used to secure the stamper
into the press. The stamper was next
trimmed to size and the back sanded
smooth to ensure a smooth finish to
the mouldings and improve contact
between the stamper and the press
die. The edge was then pressed hydraulically
to form another lip to clamp the edge
down on the press. The stampers would
be used in hydraulic presses to mould
the LP discs. The advantages of this
system over the earlier more direct
system included ability to make a
large number of records quickly by
using multiple stampers. Also, more
records could be produced from each
master since molds would eventually
wear out.
Since
the master was the unique source of
the positive, made to produce the
stampers, it was considered a library
item. Accordingly, copy positives,
required to replace worn positives,
were made from unused early stampers.
These were known as copy shells and
were the physical equivalent of the
first positive.
The
"pedigree" of any record can be traced
through the stamper/positive identities
used, by reading the lettering found
on the record run-out area.
[Author’s
note: The Association of Recorded Sound
Collectors (ARSC) has established the
ARSC Recorded Sound Discussion
List (ARSCLIST) to facilitate the exchange
of information on sound archives and
promote communication among those interested
in preserving, documenting, and making
accessible the history of recorded sound.
An ARSCLIST Thread with the subject
Metal Parts is comprised of three or
four Email messages which confirm that
the original shells consisted of electroplated
copper followed by electroplated nickel
as late as the 1940’s. The first message
reads:
"What
is the preferred method of cleaning
and storing metal parts?
I
would think that alcohol would be
a safe and effective cleaning agent
Should
anything be applied to keep them from
corroding (gun oil, perhaps)?
Weren't
fathers and stampers usually copper
with a nickel backing?"
──────────────────────────────────────────────
The
second message is:
"I
recently cleaned up an early Gramophone
Company stamper of nickel-plated copper,
which had been coated in paraffin
wax to prevent tarnishing. Following
able advice from Mark Hogan at the
National Film and Sound Archive in
Australia, I placed the stamper in
a 50/50 solution of isopropanol and
de-ionised water, bringing it up to
a temperature of 70 degrees Celsius.
The ridges (negative grooves) were
lightly brushed to loosen the melting
wax, and afterwards the disc was rinsed
in isopropanol.
In
consultation with the EMI Archive
and others, after use the stamper
wasn't recoated, but placed between
acid-free paper in a sealed container
for storage."
──────────────────────────────────────────────
The
third message read:
"All
the Victor/Bluebird, and Decca parts
I have transferred (fathers, mothers
and stampers) have been nickel-plated
copper, the nickel being the recorded
surface.
(The
film Command Performance says Victor
also employed a final plating of platinum
(!), but I find that more than a little
hard to believe.)
My
experience with parts from the 20's,
30's and 40's is that the nickel rarely
shows any signs of tarnish. In any
case, I use Noxon metal polish and
a suitable soft brush, followed by
distilled water and drying with lint-free
paper towels. My tests have shown
this treatment does not degrade the
surface in any audible way. At the
Sony Studios they are doing the same."
──────────────────────────────────────────────
The
last message says,
"I
believe record companies actually
cleaned them with naphtha. Victor
stored them vertically in large envelopes,
or so they showed in the promo film
"Command Performance"
Gun
oil might work; you need something
to keep the copper from turning green,
but removable so that the recording
itself is accessible. I don't remember
what mothers and matrices were made
from, or whether those are susceptible
to corrosion..."
──────────────────────────────────────────────
I
have confirmed the second message
above with the writer.]